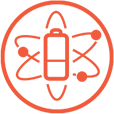
Cambridge EnerTech’s
Lithium-ion Battery Development & Commercialization
Delivering Higher Performance and Increased Productivity
MARCH 14 - 15, 2024
The lithium-ion battery (LIB) industry stands as a lucrative multibillion-dollar sector. Extensive research endeavors are dedicated to enhancing these batteries by focusing on the development of advanced anode, cathode, and electrolyte materials that can hold more charge within a given volume, consequently leading to higher energy densities. Achieving this objective necessitates a diverse and collaborative effort involving various disciplines such as chemistry, electrochemistry, materials science, physics, engineering, and manufacturing. Cambridge EnerTech's Lithium-ion Battery Development & Commercialization conference addresses these crucial aspects in translating fundamental discovery science into practical battery design, research prototyping, and efficient manufacturing processes. This holds the key to achieving rapid improvements in both performance and cost following commercialization.